Cost vs Benefits: Passive House
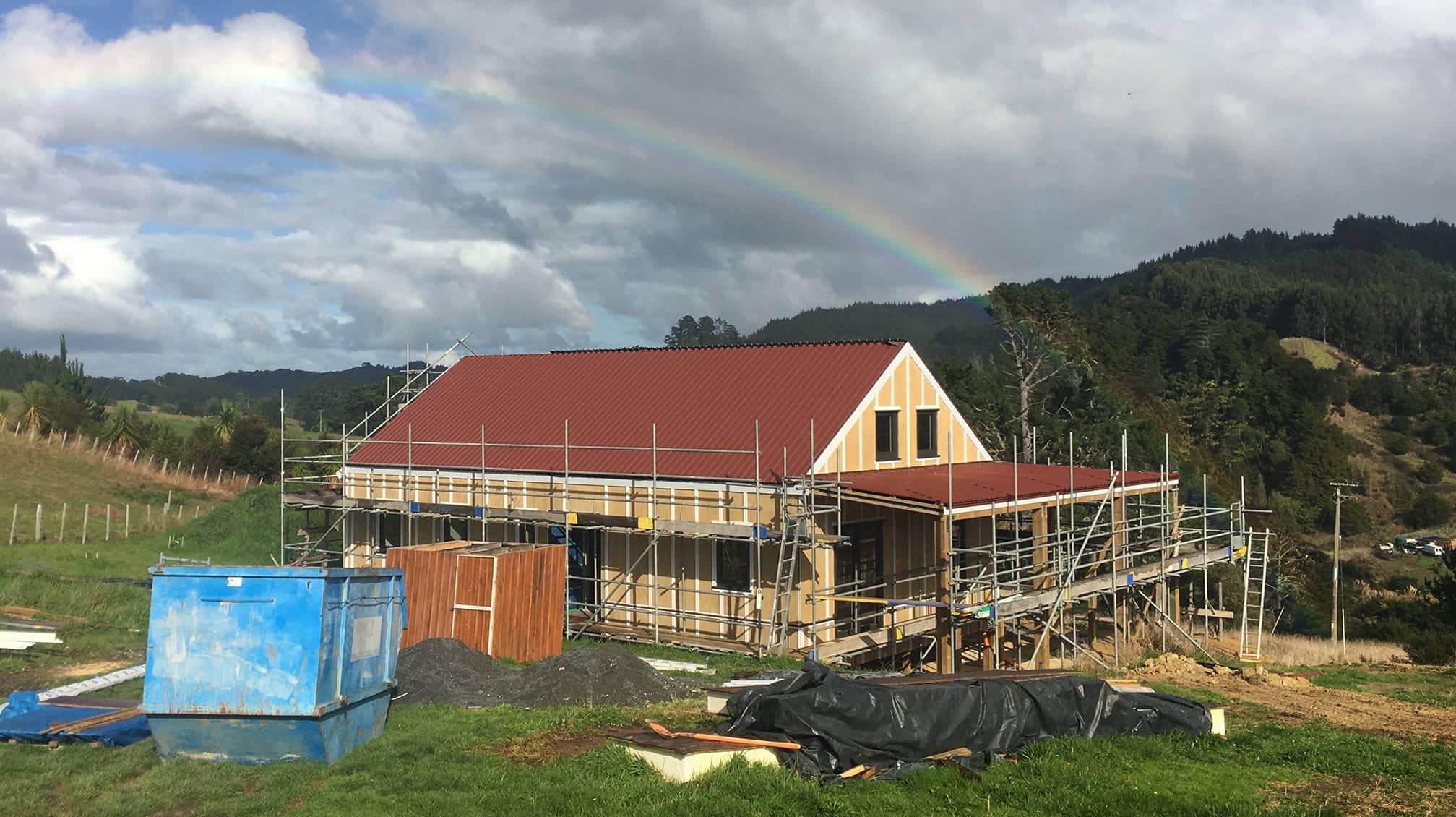
When you’re building a home, cost is inevitably at the front of your mind – particularly in today’s market, where building and material prices seem to rise each week. Respond Architect’s Joe Lyth shows us why investing more up-front will see you enjoying savings and health benefits well into the future, and how you can mitigate cost increases.
Joe has long been interested in creating more energy efficient, healthy homes. However, he’s recently become somewhat of an expert in the area – achieving his Passive House certification and designing and building his own Passive House in Tahekeroa, North of Auckland.
“I’ve experienced first-hand the stress of building from the perspective of the client, especially when it comes to cost management!” Joe says. “But I’m absolutely a firm advocate of paying for quality up front to benefit you in the long run – which is what Passive House certification is all about.”
Building to Passive House standards guarantees a home that is warmer, drier, healthier and far more energy efficient by using a scientifically calculated formula, thorough observation, and testing throughout the build. Achieving Passive House levels of efficiency is centred around five key elements: airtightness, minimal thermal bridging, ventilation, good windows and good insulation.
“If you get these elements right, you’ll create a home that is more comfortable to live in, more durable, and far cheaper to run,” says Joe. “The materials can be no different from a standard project. Passive House Certification is concerned with the result, not how you get there. While the systems and attention to detail required to achieve the certification can add cost, you can balance this by assessing the buildability of the project, simplifying or reducing the form, and balancing your priorities.”
1. Air-tightness
Airtightness refers to avoiding un-intentional air leaks. In the same way that we want water to come in through our taps instead of leaking through our roofs, we want airflow to be controlled by a ventilation system, rather than leaking through the building envelope.
If your home isn’t airtight, you’ll lose heat in winter and gain it during summer – massively impacting your heating and cooling costs. As air leaks through your building envelope it carries moisture with it. If it’s colder outside than in, this moisture will condense in the walls and insulation as it reaches the ‘dew point’ – creating the ideal conditions for mould and rot.
“Airtightness is all about energy consumption,” explains Joe. “Studies show that a standard New Zealand building code house can use anywhere from 150-275kw hours per sqm per year to heat, while a Passive House will use a maximum of 15kw hours per sqm. If you put a dollar value on that, you can see it’s basically 10-18x more expensive to heat or cool a standard house. Passive House certification guarantees the building will remain at a constant temperature for most of the year, so you should barely need to use additional heating or cooling measures.”
2. Ventilation
Ventilation and airtightness go hand-in-hand. Any building requires adequate ventilation to keep the air fresh and healthy, and the more airtight the building the more important this is.
“Ventilation provides interior air quality and ensures you’re not retaining moisture in your home. As we breathe, we release five litres of water into the air every day, and on top of this you have to consider the moisture generated by plants, pets, washing, cooking and showers. Without adequate ventilation, this moisture just sits inside and creates condensation, which can lead to mould.
“While Passive House requires a specific level of ventilation, there are no calculated ventilation requirements for a standard house under the New Zealand building code – other than an extractor in the kitchen, which often only removes fats and recirculates the air, and a fan in the bathroom which typically turns off with the lights before your shower vapor is actually removed.”
Ventilation is not just important to take moisture out, but to control the levels of C02 and VOCs (Volatile Organic Compounds, or chemicals that are given off by many modern building materials) in the air. Joe says this is where the type of ventilation unit you use can make a huge difference.
“Most Kiwi homes use either positive or negative pressure systems, which often have no filtering facility and can result in poor quality air being drawn into your home. They can also lead to moist air being pushed or pulled into openings in your walls, roof and floor, which can cause problems over time. Other systems draw air directly from the roof space, bringing with it dust and whatever else is in there – obviously not good!”
Passive Houses use a ‘balanced ducted ventilation system – made up of two fans that filter air on both the way in and out, and a heat exchanger.
“Balanced systems are the only ones to ensure air quality, durability and energy efficiency.
One fan brings fresh air in from the outside, passing it over the heat exchangerto distribute it to your living rooms and bedrooms at a comfortable temperature. The air travels across ‘transfer zones’ into your wet areas – kitchens and bathrooms – where another fan extracts it. The hot, moist air is again passed over the heat exchanger on the way out, transferring the heat to the fresh air that’s coming in. The system has 80-90% efficiency, so you’re retaining at least 80% of the heat that would otherwise be pumped outside.”
The best way to assess a building’s airtightness is to run what’s called a ‘blower door test’ – a standard for all Passive Houses. This is where a building’s windows and doors are closed and a fan put on the front door to pressurise and depressurise the house.
“The test measures air loss by calculating the number of air changes per hour – or the time it takes for the entire volume of air in the house to be exchanged for fresh air. We recently tested a new, architecturally designed home in Auckland. It recorded between 5-7 air changes per hour – a far better result than most older homes in New Zealand but still significantly worse than a Passive House, which sits at a maximum of 0.6 air changes per hour. Ultimately it shows that the air in a Passive House is far fresher, drier and healthier, and the building is far more efficient.”
3. Thermal bridging
Like airtightness, thermal bridging is to do with a building’s energy loss. There’s currently no specific requirement to consider this under New Zealand’s building code, despite the Building Act itself calling for the building envelope to ‘provide adequate thermal resistance’.
“When you build, it’s important to separate the interior and exterior with a continuous thermal envelope, and to ensure this isn’t bridged by anything that can transfer heat – such as a steel beam poking through a wall. Essentially, if you build using a material that transfers heat well, unless you have thermal breaks in place you’re going to lose heat through it and that’s going to cost you money. It will also result in cold spots inside where moisture can condense – your aluminium window frames are a perfect example of this, which can be swimming in condensation in winter!”
4. Good windows
Thermal breaks tie directly into the requirement for good quality windows. Standard windows in New Zealand are made up of one piece of aluminium containing double glazed glass. The window is installed to sit in line with the cladding, which leaves only a 1.5mm thick piece of aluminium between the inside and the outside – a substantial thermal bridge. This can get really cold in winter, causing condensation and ultimately creatingthe potential for mould, and really hot in summer, contributing to overheating. On top of this, most aluminium windows are designed to have holes in them to allow condensation to drip out – essentially creating another air leak.
“You can lose around 30% of the heat in your building through the windows,” says Joe. “By installing better windows you’ll lose significantly less heat, so while they’re a bit more expensive up front you’ll save on your long-term heating costs.”
If you do go with aluminium windows, Joe says to ensure you’re specifying ones with thermal breaks included – which are becoming more affordable as people become more aware of their importance. Alternatively, select UPVC or timber windows, which have better thermal performance. But whatever you choose, it’s important to install them correctly – with the thermal break lined up with the wall insulation to give a continuous thermal envelope.
“The glazing is equally important,” says Joe. “Double glazing, where inert gas within the glass prevents heat transfer, should be a minimum. However, standard double glazing units in New Zealand have aluminium spacers at the edge which act as a thermal bridge, so the heat just transfers through there. That’s why you often find condensation on the edge of your glass as opposed to the middle. To avoid this, try selecting double glazing that has ‘warm edge spacers’, or spacers made from materials that don’t conduct heat well, such as rubber or plastic.”
5. Insulation
When it comes to insulation options, you need to consider the R-value. ‘R’ stands for thermal resistance, or how well insulation can resist heat flow, and depends on a number of things such as the type of material used, its density and thickness.
“Essentially, the higher the R-value, the better the insulation,” says Joe. “Your insulation should be suitable for your climate – so you’d need a lower R rating in Auckland than you would in Queenstown, for example. In New Zealand the minimum R rating requirements for insulation are six times lower than they are in other countries with similar climates. It’s something the government is consulting about at the moment, so by 2035 there should be a requirement for insulation to meet Passive House levels.”
Joe says regardless of the type of insulation you use, it’s important to install it correctly and minimise the amount of timber in your walls.
“If you have holes or gaps in your insulation, your building will be full of thermal leaks. We often see electricians or plumbers installing pipes or plug sockets and removing parts of the insulation, which essentially makes it ineffective. Think about heat like water; if you have a nice, wide stream it flows slowly, whereas if you make the stream thinner it starts flowing faster. Insulation is like damming the stream up – if you have a hole in the dam, you’re going to lose water, or in this case heat, much more quickly.
“Similarly, the more timber framing you have in the wall, the less insulation you have. When you consider the wall as a whole your R2.8 insulation may only actually be achieving R1.2 due to the amount of wood! Reducing the amount of timber through careful design, insulating over the outside of the timber frame, or using SIPs or other systems can minimise this issue.”
At the end of the day, Joe says there are significant cost and health benefits to building a Passive House.
“Passive House certification is all about ensuring you don’t lose energy, so your home is a lot cheaper to run – but there are other benefits that come with this. The ‘passive’ side of it is that you don’t really need to do anything to maintain a comfortable living environment – the mechanical ventilation, correct levels of insulation and good windows do it for you. Adequate ventilation and insulation protect the fabric of your home, leading to less maintenance and repainting, and no need to replace the mouldy curtains every year!
“Having a healthier home means less days off work or school, and less doctors’ bills too. So, not only are you saving money over time, you and your family are generally healthier and happier – and what’s more important than that?”